Why are Drive-in and drive-thru Important in Industrial Warehouses
- distributionxusa
- Aug 1, 2022
- 2 min read
Given today's fast-moving, ever-changing warehouse problem many companies face, using Drive-In Rack is an effective solution to the storage space problem. DISTRIBUTION X provides businesses large and small with effective pallet rack solutions for their storage needs, regardless of the size of their warehouse facility.
Drive-in and drive-thru and pallet flow rack systems used are:
Drive-in and drive-thru
Drive In Racking and drive-thru (sometimes spelled drive-thru) is a storage rack configuration that allows forklifts to drive directly into lanes (called bays) of stacked rows. The difference between a drive-in pallet rack system and a drive-thru pallet rack system is whether there is an inlet at only one end of the bay or both ends. Drive-in rack systems use a standard basin and outlet, while Drive-Thru Rack systems have inlet points at both ends of the bay. Since drive-in rack systems have only one channel, we use the so-called LIFO (Last In, First Out) storage method. Since there is only one entrance, the last pallet is always taken out first. Drive thru racking with two separate entry points may also use FIFO (first in, first out) storage methods. In a FIFO system, pallets are loaded at one end, pushed back at the other, and placed in front of the opposite row. The first pallet placed in such a row is the first pallet drawn at the other end. Drive in racking system benefits materials with an expiration date or when storage life is a significant concern.
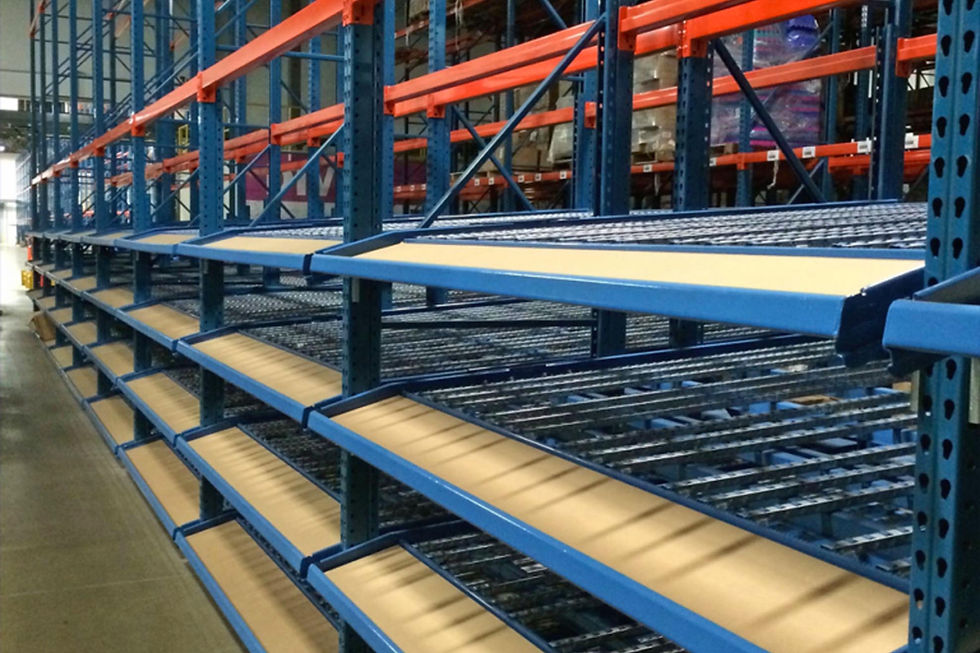
Pallet Flow System
A Pallet Flow Rack System is a high-density pallet storage system that utilizes depth to increase capacity. The system uses slightly sloping rails with rollers that allow the pallet to move smoothly along the sloping surface. These systems are also known as gravity or dynamic flow systems. Pallet flow systems often include complex speed and braking systems to control the speed of moving pallets. Pallet Flow Racking Systems are either FIFO (First In, First Out) or LIFO (Last in First Out) storage systems. If the system is loaded from the rear and unloaded from the front, it’s FIFO. Suppose the system is loaded and unloaded from the show; it’s a LIFO system.
High-density pallet storage systems have some drawbacks: access to all inventory at a given time is reduced (although this may not matter if all products stored are the same), and such a system tends to cost. Selective pallet rack systems are significantly cheaper per pallet position than high-density compatible systems. However, most media to extensive facilities requires a high-density pallet rack system. This is because it is more time efficient and optimized for costly facility space.
Conclusion
Companies must consider the most cost-effective solution to pallet rack storage problems in many scenarios. DISTRIBUTION X also provides the best Pallet Racking Repair using Demotic Racking System Repair & Reinforcement Solutions.
Comments